
To troubleshoot an Ice-O-Matic ice machine, first, check the power supply and water source. Then, inspect for any blockages or error codes.
Ice-O-Matic ice machines are renowned for their reliability, but occasional issues can arise. Ensuring your machine operates efficiently involves regular maintenance and swift troubleshooting. Common problems include power supply disruptions, water flow issues, and mechanical blockages. Identifying and resolving these problems quickly can prevent downtime and extend the lifespan of your ice machine.
Regularly inspecting the machine for error codes and cleaning components can also mitigate potential issues. Proper troubleshooting techniques can save time and money, keeping your ice machine in optimal condition. This guide aims to provide practical steps for effective troubleshooting, ensuring continuous and efficient ice production.
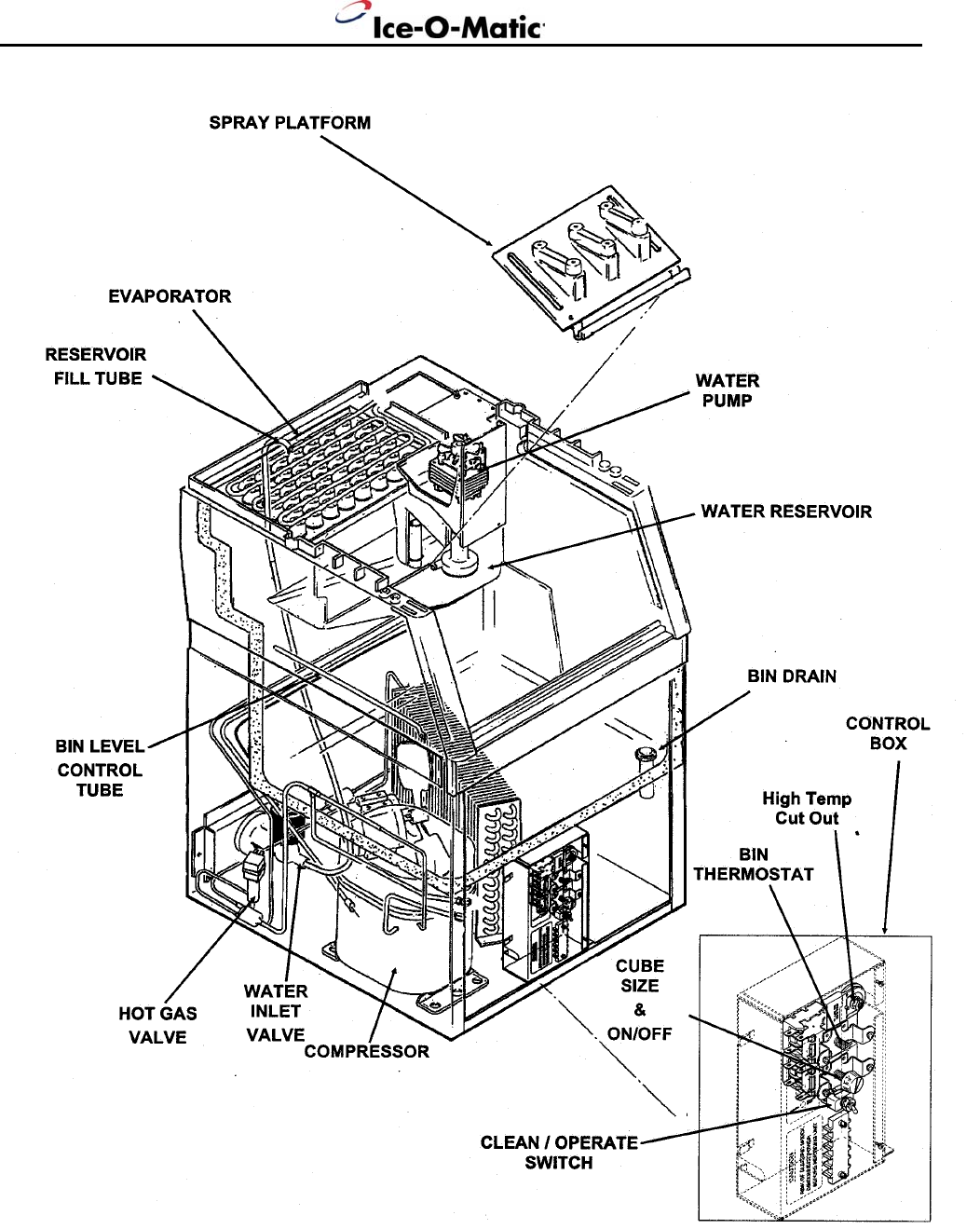
Credit: kitchen.manualsonline.com
Common Issues
Ice-O-Matic ice machines are reliable, but sometimes they have issues. Knowing the common problems helps in quick troubleshooting. Below are some frequent issues you might face.
No Ice Production
If your Ice-O-Matic machine stops making ice, check the power supply first. Ensure the machine is properly plugged in and switched on. If the power supply is fine, inspect the water supply. Make sure the water valve is open and water flows freely.
Another cause for no ice production could be the ice level sensor. The sensor might be dirty or malfunctioning. Clean the sensor with a soft cloth. If cleaning doesn’t work, consider replacing the sensor.
Possible Cause | Solution |
---|---|
Power Supply Issue | Check and ensure it’s connected |
Water Supply Issue | Verify water valve is open |
Dirty Ice Level Sensor | Clean the sensor |
Faulty Ice Level Sensor | Replace the sensor |
Slow Ice Making
Slow ice production can be frustrating. First, check the machine’s temperature settings. The ideal temperature for ice making is between 32°F and 40°F. If the temperature is too high, adjust it accordingly.
Another factor is the cleanliness of the machine. A dirty machine can slow down ice production. Regularly clean the ice machine, including the condenser coils and water lines. Use a soft brush and mild detergent.
Water quality also impacts ice production speed. Hard water can cause scale buildup. Use a water filter to reduce minerals in the water. Replace the filter every six months for optimal performance.
- Temperature Settings: Adjust to 32°F – 40°F
- Machine Cleanliness: Clean coils and water lines
- Water Quality: Use and replace water filter
By addressing these common issues, you can maintain your Ice-O-Matic ice machine. This ensures smooth and efficient ice production.
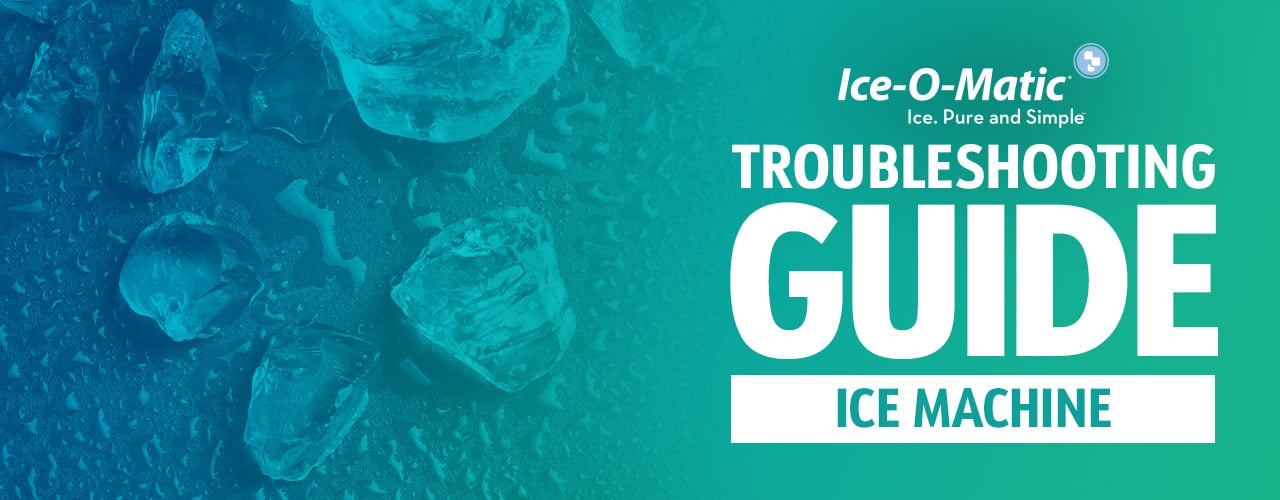
Credit: www.webstaurantstore.com
Basic Maintenance
Basic maintenance of your Ice-O-Matic ice machine ensures it runs smoothly. Regular care prevents malfunctions and extends the machine’s lifespan. This section covers essential maintenance steps.
Regular Cleaning
Regular cleaning is vital. Clean the ice machine every six months. Use a mild cleaner and soft cloth. Avoid harsh chemicals that can damage parts.
- Turn off the machine and unplug it.
- Remove ice and water from the bin.
- Use a soft cloth to wipe surfaces.
- Clean the condenser coils with a brush.
Keeping the machine clean prevents bacteria buildup and ensures ice quality.
Filter Replacement
Replacing filters is crucial. Filters remove impurities from water. Change filters every six months.
- Turn off the water supply.
- Locate the filter housing.
- Remove the old filter.
- Install the new filter.
- Turn on the water supply.
Using clean filters keeps ice tasting fresh and machine parts free from deposits.
Water Supply Problems
Water supply problems can disrupt the performance of your Ice-O-Matic ice machine. Ensuring a steady water flow is crucial. This section covers the key areas to check.
Check Water Line
A clogged or kinked water line can hinder water flow. Inspect the water line for any visible damage. Ensure it is straight and free from obstructions.
- Turn off the water supply.
- Detach the water line from the machine.
- Examine the line for kinks or clogs.
- If clogged, clean it thoroughly.
- Reconnect the water line securely.
Ensuring the water line is intact can prevent many issues.
Inspect Water Valve
The water valve controls the water flow into the machine. A faulty valve can disrupt ice production. Here’s how to inspect it.
- Turn off the power to the machine.
- Locate the water valve at the back.
- Check for any signs of wear or damage.
- Ensure the valve is not blocked.
- If necessary, replace the valve.
Regular inspections of the water valve can ensure optimal performance.
Issue | Solution |
---|---|
Kinked Water Line | Straighten the line |
Clogged Water Line | Clean the line |
Faulty Water Valve | Replace the valve |
Addressing water supply problems can significantly improve your ice machine’s efficiency.
Electrical Issues
Electrical issues with your Ice-O-Matic ice machine can disrupt its performance. Identifying and fixing these issues ensures your machine runs smoothly.
Power Supply Check
First, verify if the ice machine is getting power. Check the power cord for any visible damage. Ensure it is plugged into a working outlet. Use a multimeter to test the outlet voltage.
Step | Action |
---|---|
1 | Inspect power cord for damage. |
2 | Confirm the plug is securely in the outlet. |
3 | Test the outlet with a multimeter. |
If the outlet is not working, try another outlet. Ensure the circuit breaker hasn’t tripped.
Control Board Reset
The control board is crucial for the ice machine’s operation. A simple reset might fix many electrical issues.
- Turn off the ice machine.
- Unplug the machine from the power source.
- Wait for 5 minutes.
- Plug the machine back in.
- Turn on the machine.
This reset process can resolve minor glitches. If the issue persists, inspect the control board for any visible damage or loose connections.
For any severe electrical issues, consider contacting a professional technician.
Temperature Concerns
Temperature plays a crucial role in your Ice-O-Matic Ice Machine’s performance. High or low temperatures can affect ice production. Addressing temperature concerns ensures your machine runs smoothly.
Ambient Temperature
Ambient temperature impacts your ice machine’s efficiency. The room temperature should stay between 50°F and 90°F. Temperatures outside this range can cause problems.
If the room is too hot, the machine works harder. This can lead to overheating and reduced ice production. Ensure proper ventilation around your machine.
Conversely, if the room is too cold, the machine might freeze up. This can damage internal components. Keep the room within the ideal temperature range.
Condenser Coil Cleaning
Condenser coils play a vital role in cooling. Dirty coils reduce efficiency and increase energy consumption. Clean the coils regularly to maintain optimal performance.
Use the following steps to clean the condenser coils:
- Turn off and unplug the machine.
- Remove the front panel to access the coils.
- Use a brush or vacuum to remove dust and debris.
- Wipe the coils with a damp cloth.
- Reassemble the front panel and plug in the machine.
Clean the coils every three months for best results. Regular maintenance extends the lifespan of your ice machine.

Credit: www.culinarydepotinc.com
Mechanical Failures
Dealing with mechanical failures in your Ice-O-Matic ice machine can be frustrating. These issues often stem from malfunctioning components. This guide will help you troubleshoot common mechanical failures.
Inspect Auger Motor
The auger motor drives the ice-making process. A faulty auger motor can stop ice production. To inspect the auger motor:
- Disconnect the machine from the power source.
- Remove the panels to access the motor.
- Check for any visible damage or loose connections.
- Use a multimeter to test the motor’s electrical continuity.
- If the motor is damaged, replace it.
Regular inspection helps maintain the auger motor’s performance. Always ensure the motor is clean and free of debris.
Check Ice Bin Sensor
The ice bin sensor monitors the ice level in the bin. A malfunctioning sensor can cause the machine to stop making ice. To check the ice bin sensor:
- Turn off and unplug the machine.
- Locate the ice bin sensor inside the bin.
- Inspect the sensor for any dirt or blockage.
- Clean the sensor with a soft cloth.
- Test the sensor by moving ice around it and observing if it responds.
A clean and functional ice bin sensor ensures efficient ice production. Replace the sensor if it does not respond correctly.
Component | Action | Tools Needed |
---|---|---|
Auger Motor | Inspect and test | Multimeter |
Ice Bin Sensor | Clean and test | Soft cloth |
Maintaining your Ice-O-Matic ice machine involves regular checks and cleanings. This ensures a continuous supply of ice.
Error Codes
Understanding Error Codes on your Ice-O-Matic ice machine is crucial. These codes provide insights into potential issues. This section will help you read, reset, and resolve these codes.
Deciphering Codes
Error codes on Ice-O-Matic machines are like secret messages. Each code points to a specific problem. Here’s a table to help you understand some common codes:
Error Code | Description |
---|---|
E01 | Water supply issue |
E02 | High-temperature alert |
E03 | Ice bin full |
E04 | Low refrigerant |
Reset Procedures
Resetting your Ice-O-Matic machine can clear error codes. Follow these steps to reset your machine:
- Turn off the machine.
- Unplug from the power source.
- Wait for 5 minutes.
- Plug it back in.
- Turn the machine on.
If the error persists, consult the user manual. This can help you further diagnose the issue.
Professional Help
Sometimes, Ice-O-Matic ice machines need more than basic troubleshooting. In such cases, seeking professional help becomes necessary. Knowing when to call a technician can save time and prevent further damage. Below are some guidelines to help you decide.
When To Call A Technician
- If the machine makes strange noises.
- When the ice output is low or inconsistent.
- If there is water leakage from the machine.
- When the machine does not power on.
- If there are electrical issues.
Calling a technician ensures the problem is diagnosed correctly. This prevents further complications and maintains the machine’s longevity.
Warranty Considerations
Always check your Ice-O-Matic machine’s warranty before seeking repairs. Warranty coverage may save you from out-of-pocket expenses. Here are some key points to consider:
Item | Warranty Period | Coverage Details |
---|---|---|
Parts | 3 Years | Manufacturing defects |
Labor | 1 Year | Service and repairs |
Compressor | 5 Years | Replacements |
Contact Ice-O-Matic for warranty validation before hiring a technician. This ensures your repairs fall under the warranty coverage.
Frequently Asked Questions
How To Reset Ice-o-matic Ice Machine?
To reset your Ice-O-Matic ice machine, locate the reset button. Press and hold it for a few seconds. This should restart the machine and resolve minor issues.
Why Is Ice-o-matic Not Making Ice?
If your Ice-O-Matic isn’t making ice, check for power supply issues. Ensure the water line is connected. Clean the machine to remove any blockages or debris.
How To Clean Ice-o-matic Ice Machine?
To clean your Ice-O-Matic ice machine, use a manufacturer-approved cleaner. Follow the instructions in the user manual. Regular cleaning prevents blockages and maintains ice quality.
What To Do If Ice-o-matic Leaks Water?
If your Ice-O-Matic leaks water, inspect the water lines for leaks. Tighten any loose connections. Ensure the drain is not clogged to prevent overflow.
Conclusion
Regular maintenance keeps your Ice-O-Matic ice machine running smoothly. Address issues promptly to avoid downtime. Follow our troubleshooting tips to ensure optimal performance. Proper care extends the machine’s lifespan. Enjoy consistent ice production by staying proactive. Keep your business running efficiently with a well-maintained ice machine.
Thank you for reading our troubleshooting guide.