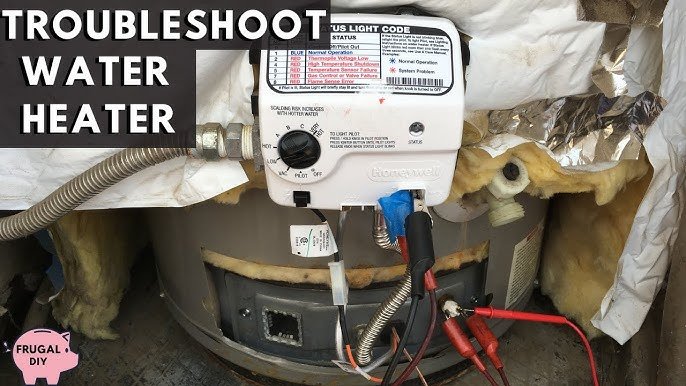
For Honeywell gas valve troubleshooting, first check the power supply and ensure the valve is receiving voltage. Next, inspect for any blockages or leaks that may affect operation.
Troubleshooting a Honeywell gas valve can be straightforward with the right approach. These valves are vital for controlling gas flow in heating systems, making effective troubleshooting essential. Common issues include failure to open or close, inconsistent operation, and strange noises.
Identifying the root cause of these problems saves time and reduces repair costs. Understanding the basic functions of the gas valve is crucial for effective troubleshooting. Whether you are a homeowner or a professional technician, knowing how to address common issues can enhance safety and efficiency. This guide offers practical tips to help you quickly diagnose and resolve Honeywell gas valve problems.
Introduction To Honeywell Gas Valves
Honeywell gas valves are essential components in many heating systems. They control the flow of gas to burners. Proper functioning ensures safety and efficiency. Understanding these valves helps in troubleshooting and maintenance.
Role In Home Heating Systems
Honeywell gas valves play a crucial role in home heating. They manage gas flow in furnaces, water heaters, and boilers. Here are some key functions:
- Gas Regulation: They regulate gas pressure and flow.
- Safety: They prevent gas leaks and ensure safe operation.
- Ignition Control: They help in igniting burners effectively.
Without these valves, heating systems cannot operate safely. Regular checks are vital for optimal performance.
Common Models And Applications
Many Honeywell gas valve models are available. Each serves specific applications. Here are some popular models:
Model | Application | Features |
---|---|---|
VR8200A | Furnaces | Automatic safety shutoff |
V4043H | Water Heaters | High efficiency |
VR8305 | Boilers | Compact design |
Choosing the right model is crucial for performance. Each model has unique features that enhance functionality. Knowing the application helps in selecting the right valve.

Credit: kcwaterheater.com
Symptoms Of A Faulty Gas Valve
Recognizing the symptoms of a faulty gas valve is crucial for safety. A malfunctioning valve can cause serious issues in your heating system. Here are the key signs to watch for.
Ignition Failures
Ignition failures are a common symptom of a faulty gas valve. This can lead to your appliance not starting at all. Here are some signs:
- Appliance doesn’t ignite after several attempts
- Clicking sound without ignition
- Flame goes out immediately after lighting
These issues suggest that the gas valve may not be opening correctly. It’s essential to address this promptly to avoid further complications.
Inconsistent Flame Patterns
Inconsistent flame patterns can indicate problems with your gas valve. A healthy flame should be steady and blue. Look for these signs:
- Yellow or orange flames
- Flames flickering or dancing
- Flame height varying significantly
Such irregularities may suggest that gas flow is obstructed. This can lead to inefficient heating and potential safety hazards.
Safety Precautions
Ensuring safety during Honeywell gas valve troubleshooting is vital. Follow these precautions to avoid accidents and ensure a secure environment.
Shutting Off The Gas Supply
Before starting any troubleshooting, shut off the gas supply. This step protects against leaks and potential fires.
- Locate the gas shutoff valve.
- Turn the valve clockwise to close it.
- Confirm the gas is off by checking appliances.
It’s crucial to wait for any residual gas to dissipate before proceeding.
Avoiding Diy Hazards
Handling gas valves can be dangerous. Always take precautions to avoid hazards.
- Wear protective gloves and goggles.
- Ensure the area is well-ventilated.
- Use tools designed for gas appliances.
Never attempt complex repairs without professional help. Always prioritize safety over convenience.
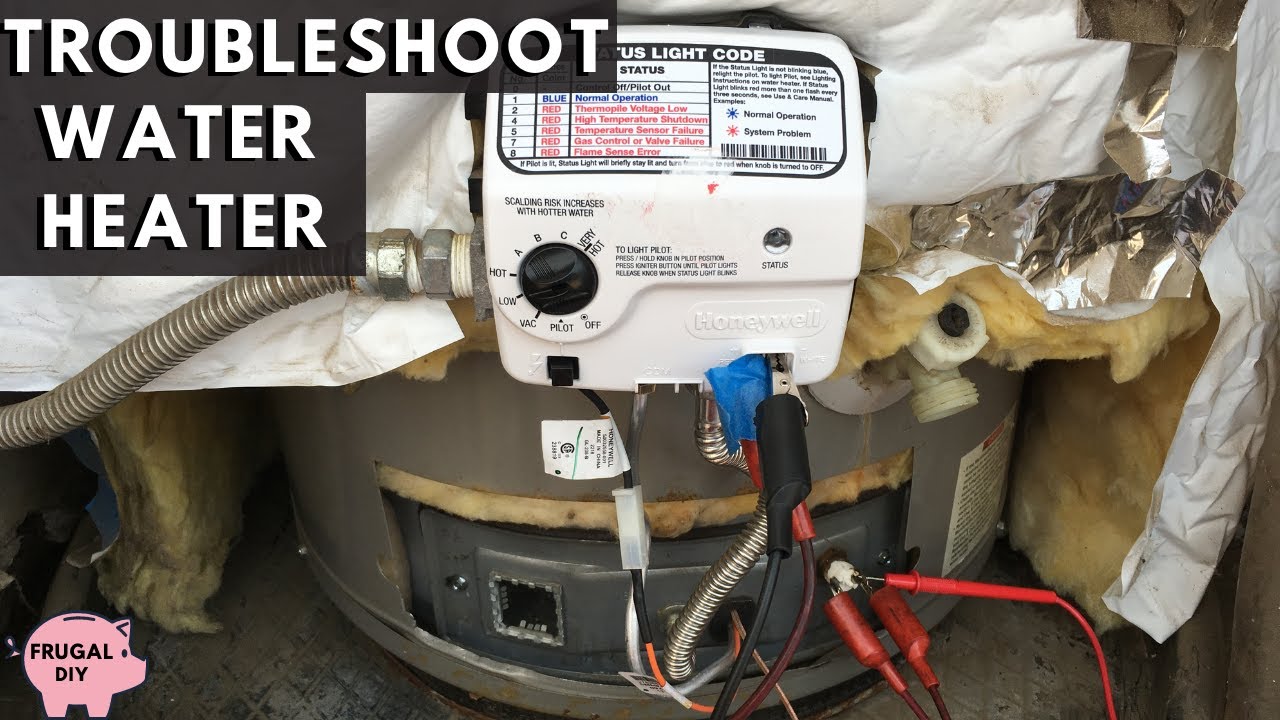
Credit: www.youtube.com
Basic Troubleshooting Steps
Gas valves are crucial for safe appliance operation. If issues arise, follow these basic troubleshooting steps. They help identify common problems quickly and efficiently.
Visual Inspections
Start with a thorough visual inspection of the gas valve. Look for signs of damage or wear. Pay attention to the following:
- Cracks or breaks in the valve housing
- Corrosion on metal parts
- Loose connections or fittings
- Foreign objects obstructing the valve
Use a flashlight for better visibility. Clean any dirt or debris around the valve. Ensure all connections are tight. This helps prevent leaks.
Checking For Error Codes
Many Honeywell gas valves display error codes. These codes provide vital information about the problem. Follow these steps to check for error codes:
- Locate the valve’s digital display.
- Press the reset button, if available.
- Observe the display for error codes.
Refer to the user manual for code meanings. Common error codes include:
Error Code | Meaning |
---|---|
E1 | Gas flow issue |
E2 | Temperature sensor failure |
E3 | Pressure switch fault |
After noting any error codes, reset the valve. This may resolve minor issues.
Common Issues And Quick Fixes
Gas valves can cause various problems. Knowing these issues helps you fix them quickly. Below are common problems and their simple solutions.
Pilot Light Problems
The pilot light is essential for gas valves. If it goes out, the system won’t work. Here are some common pilot light issues:
- Extinguished Pilot Light: Dust or debris may block the flame.
- Weak Flame: Low gas pressure can cause a weak flame.
- Flame Color: A yellow or orange flame indicates a problem.
Quick Fixes:
- Check for obstructions around the pilot light.
- Clean the pilot orifice with compressed air.
- Adjust gas pressure if the flame is weak.
- Use a flame sensor to ensure proper ignition.
Adjusting The Pressure Regulator
A pressure regulator controls the gas flow. If it fails, it can lead to issues.
Issue | Symptoms | Quick Fix |
---|---|---|
Low Pressure | Appliance does not heat properly. | Adjust the regulator settings. |
High Pressure | Gas leaks or hissing sounds. | Check and tighten connections. |
Inconsistent Pressure | Appliance cycles on and off. | Replace the regulator if faulty. |
Follow these steps to adjust the pressure regulator:
- Locate the pressure adjustment screw.
- Use a screwdriver to turn the screw.
- Monitor the appliance for proper operation.
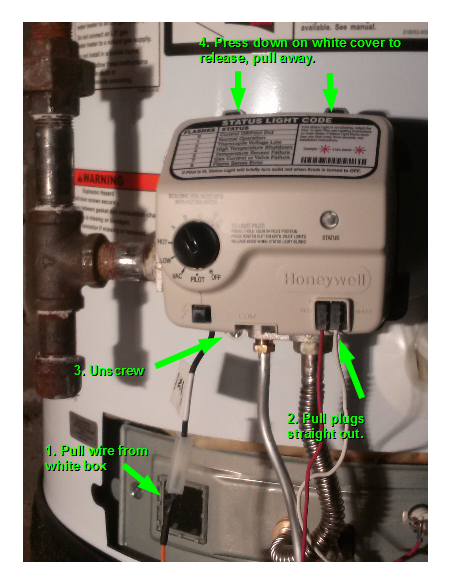
Credit: tylertork.com
When To Call A Professional
Understanding when to call a professional for Honeywell gas valve troubleshooting is crucial. Some issues require expert knowledge. Attempting repairs without proper skills can lead to safety risks.
Complex Repairs
Some repairs are too complex for DIY efforts. Here are signs to call a professional:
- Gas leaks detected.
- Valves not responding to adjustments.
- Unusual noises from the gas system.
- Frequent pilot light outages.
- Burner flames are not blue.
These issues may indicate deeper problems. Professionals have the tools and expertise to diagnose correctly. They ensure safety and compliance with regulations.
Warranty Considerations
Check your warranty before making repairs. Some warranties require professional servicing. DIY repairs can void your warranty. Here are points to remember:
- Review warranty documentation.
- Contact the manufacturer for guidance.
- Keep records of all repairs.
Protect your investment. Calling a professional can save money in the long run. Ensure your Honeywell gas valve remains under warranty.
Maintenance Tips For Longevity
Proper maintenance enhances the lifespan of your Honeywell gas valve. Regular care prevents issues and ensures efficient performance. Follow these tips for optimal longevity.
Regular Cleaning
Cleaning your gas valve can prevent dirt buildup. Follow these steps for effective cleaning:
- Turn off the power to the gas valve.
- Remove the cover carefully.
- Use a soft cloth to wipe the exterior.
- Check for any debris inside the valve.
- Use compressed air to blow out dust.
Regular cleaning helps maintain smooth operation. Schedule cleaning every 6 months.
Seasonal Inspections
Seasonal inspections are vital. They help catch problems early. Follow this checklist for your inspection:
- Check for leaks around the valve.
- Inspect the wiring for any damage.
- Test the functionality of the valve.
- Ensure the thermostat is working correctly.
- Look for signs of rust or corrosion.
Conduct these inspections before the heating season. This ensures safety and efficiency.
Upgrading Your Gas Valve
Upgrading your Honeywell gas valve can improve safety and efficiency. Modern valves feature advanced technology that enhances performance. Choosing the right upgrade can make a big difference.
New Features In Modern Valves
Modern Honeywell gas valves come with innovative features. These include:
- Improved Safety: Enhanced shut-off mechanisms prevent leaks.
- Smart Technology: Remote monitoring for better control.
- Energy Efficiency: Reduced energy consumption.
- Durability: Built with high-quality materials.
These features lead to better performance and longer lifespan.
Compatibility And Installation
Compatibility is crucial for a successful upgrade. Check the specifications of your current system. Ensure the new valve matches these specifications.
Installation steps include:
- Turn off the gas supply.
- Remove the old valve carefully.
- Install the new valve according to the manual.
- Reconnect the gas supply and check for leaks.
Using a professional for installation is always a good idea. They ensure everything is done safely and correctly.
Frequently Asked Questions
What Are Common Honeywell Gas Valve Issues?
Common issues with Honeywell gas valves include improper operation, failure to open or close, and erratic flame behavior. These problems can arise from electrical malfunctions, dirt buildup, or faulty components. Regular maintenance and proper installation can help prevent these issues and ensure smooth operation.
How To Reset A Honeywell Gas Valve?
To reset a Honeywell gas valve, first turn off the power and gas supply. Wait a few minutes, then turn the gas back on. Finally, restore power to the valve. This simple procedure can resolve minor issues and restore functionality to the system.
Why Is My Honeywell Gas Valve Not Opening?
If your Honeywell gas valve is not opening, it may be due to electrical issues, a faulty thermostat, or a blockage in the gas line. Inspect wiring and connections for damage. If the problem persists, consider consulting a professional for a thorough inspection and necessary repairs.
How To Test A Honeywell Gas Valve?
To test a Honeywell gas valve, use a multimeter to check voltage at the terminals. Ensure the valve receives the correct voltage when activated. If there’s no voltage, investigate the power source or thermostat. If voltage is present but the valve doesn’t open, it may need replacement.
Conclusion
Troubleshooting your Honeywell gas valve can save time and money. Regular maintenance is key to preventing issues. Always consult the manual for specific guidance. If problems persist, consider reaching out to a professional. Staying informed will help you keep your system running efficiently and safely.
Your home deserves the best care.