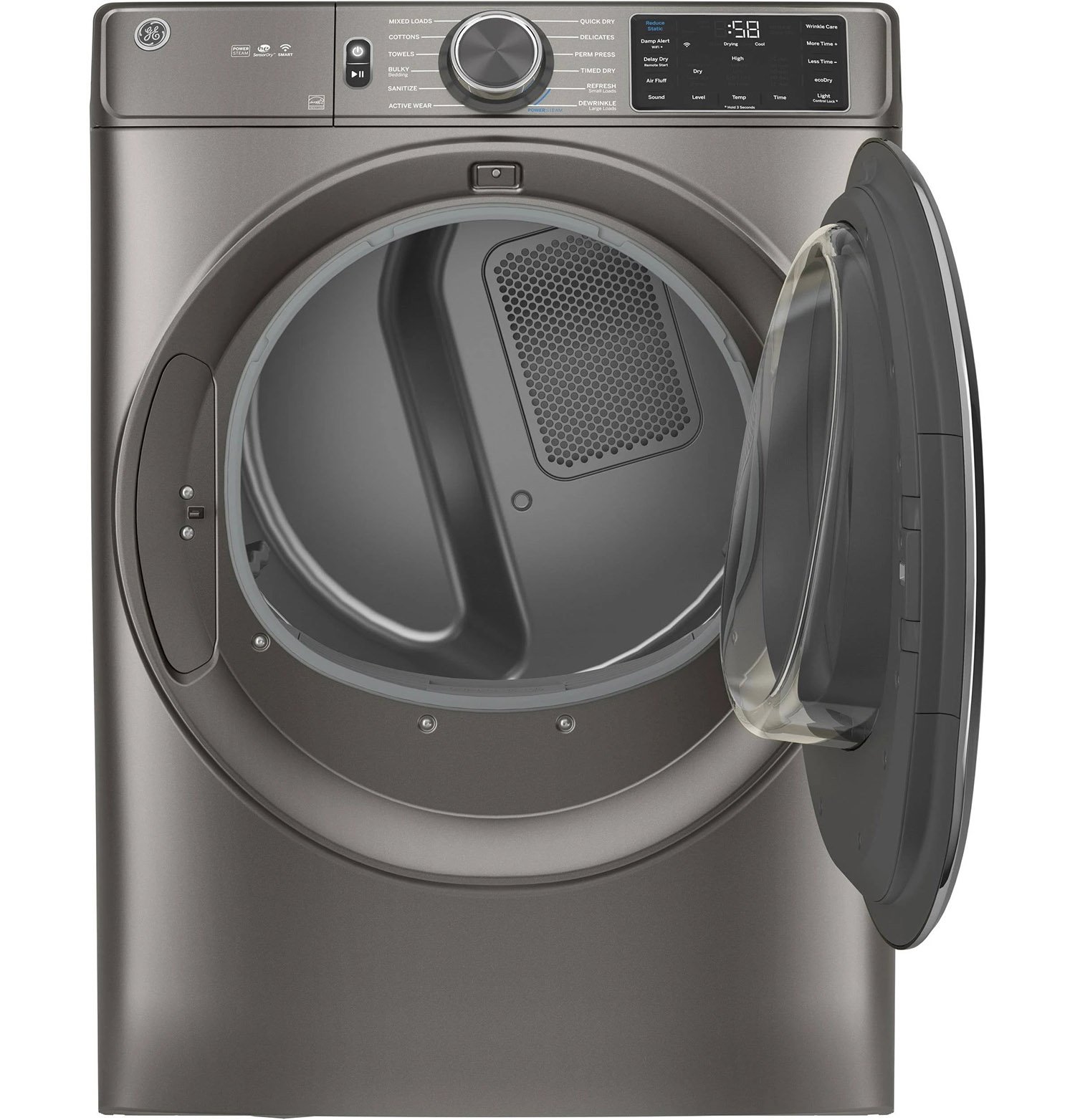
If your GE Sensor Dry dryer is experiencing issues, start by checking the power supply and ensuring the door is properly closed. Look for any error codes on the display, and clean the lint filter and exhaust vent to improve drying performance.
Also, consider checking the moisture sensor and the timer settings to ensure they are functioning correctly. If you’re still experiencing problems, refer to the user manual for specific troubleshooting steps or contact GE customer support for further assistance. A GE Sensor Dry dryer is a convenient appliance for drying clothes efficiently.
However, like any machine, it may encounter occasional issues. We will discuss common troubleshooting steps for addressing problems with the GE Sensor Dry dryer. By following these tips, you can quickly identify and resolve issues, ensuring your dryer operates at its best. Let’s explore some practical solutions to troubleshoot your GE Sensor Dry dryer and get it back to optimal performance.
Checking The Power Supply
When your GE Sensor Dry dryer is not functioning properly, it’s important to start troubleshooting by checking the power supply. Many issues can be traced back to problems with the power source. Here’s a step-by-step guide to help you diagnose the power supply-related problems with your dryer.
Circuit Breaker
Start by checking the circuit breaker in your home’s electrical panel. Make sure to switch the breaker for the dryer to the “off” position, then back to the “on” position. Be sure to look for any signs of a tripped breaker, such as a switch that’s in the middle or a position that doesn’t align with the other breakers. If you find a tripped breaker, reset it and check if the dryer powers on.
Power Outlet
Next, inspect the power outlet where the dryer is plugged in. Ensure that the outlet is supplying power by plugging in another electronic device or using a voltage tester. Look for any burn marks, frayed wires, or other signs of damage. If the outlet appears to be faulty, it may need to be replaced by a qualified electrician.
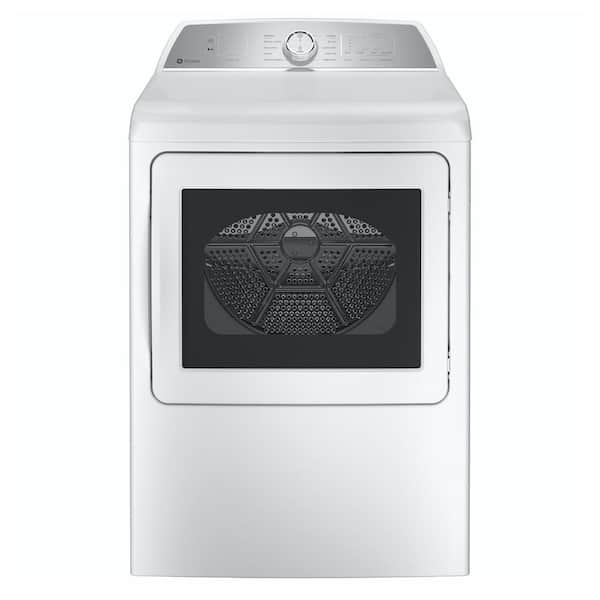
Credit: www.homedepot.com
Inspecting The Heating Element
When troubleshooting your GE Sensor Dry dryer, inspecting the heating element is an essential step to identify potential issues. The heating element plays a crucial role in drying your clothes effectively. In this section, we will discuss how to visually examine the heating element and use a multimeter to ensure it’s working properly.
Visual Examination
Begin by visually inspecting the heating element to check for any visible signs of damage or malfunction. Follow these steps:
- Unplug the dryer to ensure safety.
- Locate the heating element within the dryer cabinet.
- Check for any visible breaks, burns, or corrosion on the element.
- Inspect the wiring connected to the heating element for any damage.
- Ensure there are no obstructions or blockages affecting the airflow around the heating element.
Using A Multimeter
If the visual inspection doesn’t identify any visible issues, using a multimeter can help determine the functionality of the heating element. Follow these steps to use a multimeter:
- Set the multimeter to the continuity or resistance setting.
- Disconnect the wires from the heating element to perform the test.
- Place the multimeter probes on the terminals of the heating element.
- A reading of zero or very low resistance indicates that the heating element is functioning properly.
- If the multimeter shows no continuity or a high resistance reading, it indicates a faulty heating element that needs to be replaced.
Evaluating The High-limit Thermostat
Evaluating the high-limit thermostat is crucial when troubleshooting the GE Sensor Dry dryer. This component plays a vital role in maintaining the temperature within safe limits during the drying process. By understanding how to identify and test the high-limit thermostat, you can effectively address issues related to overheating or underheating in your dryer.
Identifying
When evaluating the high-limit thermostat, start by locating it within the dryer. In most models, the high-limit thermostat is situated on the heating element housing. It is a small, round device with two wires connected to it. Refer to the dryer’s manual or schematic diagram to pinpoint the exact location of the high-limit thermostat.
Testing
Before testing the high-limit thermostat, ensure the dryer is unplugged to avoid any electrical hazards. Using a multimeter, set it to the Rx1 setting to measure for continuity. Remove the wires connected to the thermostat and place the multimeter probes on the terminals. If the multimeter displays a reading of infinity, the thermostat is faulty and needs to be replaced. If there is continuity, the high-limit thermostat is functioning properly.
Examining The Belt
When it comes to troubleshooting a GE Sensor Dry dryer, one crucial area to examine is the belt. A malfunctioning belt can lead to various issues such as the dryer not turning or uneven drying. In this section, we will explore the steps to visually inspect the belt and assess its tension.
Visual Inspection
Begin by visually inspecting the belt for any signs of wear, fraying, or damage. Check for any visible cracks or separation. A worn-out belt may appear stretched or loose. It’s essential to ensure the belt is properly aligned and in good condition. Make sure the dryer is unplugged before proceeding with this examination.
Tension Assessment
Assessing the tension of the belt is crucial for smooth dryer operation. Check the tension by gently pressing on the belt. It should offer resistance and have a minimal amount of give. If the belt seems loose or overly flexible, it may need to be replaced. The optimal tension allows the belt to grip the drum effectively, enabling proper rotation without slipping.
Verifying The Motor
When experiencing issues with the GE Sensor Dry dryer, the motor is a crucial component to examine. Verifying the motor’s functionality is a key step in troubleshooting and resolving any potential problems. In this section, we will delve into the process of diagnosing the motor’s functionality and verifying its shaft, which are essential in ensuring that the dryer operates optimally.
Functionality Diagnosis
Properly diagnosing the functionality of the motor involves a systematic approach to rule out any potential issues. Follow these steps to effectively assess the motor’s performance:
- Check the power supply: Verify that the dryer is receiving adequate power supply. A malfunctioning power source can impede the motor’s functionality.
- Inspect the wiring: Examine the wiring connections to ensure they are secure and free from any damage. Loose or damaged wires can disrupt the motor’s operation.
- Test the start switch: Evaluate the start switch to ensure it is engaging properly. A faulty start switch can prevent the motor from initiating.
Shaft Verification
Verifying the motor’s shaft is paramount in maintaining the dryer’s efficiency. A misaligned or damaged shaft can lead to operational issues. Here’s how to assess the shaft:
- Inspect for misalignment: Check if the motor shaft is aligned with the drum and pulley. Misalignment can cause excessive wear and tear.
- Lubrication assessment: Ensure that the shaft is adequately lubricated to facilitate smooth rotation. Insufficient lubrication can lead to friction and overheating.
Clean Lint Trap And Vent
When it comes to troubleshooting your GE Sensor Dry dryer, one common issue that can cause disruptions in the drying process is a dirty lint trap and vent. Proper maintenance of these components is crucial to ensure the dryer functions efficiently and safely. In this section, we will explore the importance of cleaning the lint trap and vent, along with essential steps for doing so.
Lint Trap Maintenance
Regular maintenance of the lint trap is essential to prevent lint buildup, which can hinder the dryer’s performance and pose a fire hazard. To clean the lint trap, follow these simple steps:
- After every drying cycle, remove the lint screen from the dryer.
- Gently remove the accumulated lint from the screen.
- Use a soft-bristled brush or vacuum attachment to clear any remaining lint from the screen.
- Periodically wash the lint trap with warm, soapy water to remove any residue or fabric softener buildup. Be sure to dry it thoroughly before reinserting it into the dryer.
Ventilation Inspection
A clogged or obstructed dryer vent can lead to inefficiency and even safety concerns. Regular inspection and cleaning of the dryer vent are crucial for optimal performance. Here’s how to conduct a ventilation inspection:
- Disconnect the dryer from the power source and move it away from the wall to access the vent duct.
- Inspection the vent for any signs of blockage, such as lint buildup or debris.
- If the vent appears clogged, use a vent brush or vacuum attachment to carefully remove the obstructions.
- Ensure that the vent duct is properly connected and free of any kinks or damage that could restrict airflow.
- Once the inspection and cleaning are complete, reconnect the dryer and test its operation to ensure proper ventilation.
By regularly cleaning the lint trap and inspecting the ventilation system, you can maintain the efficiency and safety of your GE Sensor Dry dryer. These simple maintenance tasks can help prevent issues and ensure smooth operation for years to come.
Monitoring The Moisture Sensor
Monitoring the moisture sensor in your GE Sensor Dry dryer is essential for ensuring efficient and effective drying performance. The moisture sensor plays a crucial role in detecting the level of moisture in the clothes, allowing the dryer to automatically adjust the drying time for optimal results. However, if the moisture sensor is dirty or faulty, it can lead to drying issues. Hence, it’s important to properly monitor, clean, and test the moisture sensor regularly to maintain the dryer’s performance.
Sensor Location
The moisture sensor in your GE Sensor Dry dryer is typically located inside the dryer drum. It is usually positioned near the front of the drum, often near the lint filter or the door. The exact location may vary depending on the dryer model, so refer to your dryer’s manual for specific details.
Cleaning And Testing
Proper cleaning and testing of the moisture sensor are essential to ensure accurate drying. Here’s how you can clean and test the sensor:
- Cleaning:
- Unplug the dryer and locate the moisture sensor inside the drum.
- Carefully remove any lint, debris, or residue that may have accumulated on the sensor using a soft bristle brush or a cloth. Ensure that the sensor is free from any obstructions or buildup.
- Testing:
- Plug the dryer back in and select a high heat drying cycle.
- Place a damp cloth or a load of wet clothes in the dryer and start the cycle.
- Observe the drying process. The dryer should stop automatically when the clothes are dry. If the dryer continues to run longer than necessary, it may indicate a problem with the moisture sensor.
- If you suspect an issue, consider contacting a certified technician for further inspection and repairs.
Calibrating The Moisture Sensor
Calibrating the moisture sensor in your GE Sensor Dry dryer is a crucial step to ensure that your appliance operates efficiently and dries your clothes effectively. Proper calibration allows the dryer to accurately detect the moisture level in the load and adjust the drying time accordingly. If you are experiencing issues with your dryer not drying clothes properly, calibrating the moisture sensor could be the solution.
Adjustment Procedure
Before attempting to calibrate the moisture sensor, it’s important to make sure the dryer is unplugged and disconnected from the power source. You will need a Phillips screwdriver to access the sensor bars located inside the dryer drum. The adjustment procedure involves adjusting the position of the sensor bars to ensure they make proper contact with the clothes during the drying cycle.
Follow these steps to adjust the moisture sensor:
- Remove any clothes or items from the dryer drum.
- Locate the moisture sensor bars inside the drum. These are usually two metal strips located near the front of the drum.
- Loosen the screws securing the sensor bars in place using a Phillips screwdriver.
- Gently move the sensor bars closer to the drum or further apart, ensuring they make good contact with the clothes. Tighten the screws to secure the new position.
- Plug the dryer back in and test it by running a load of laundry to see if the sensor is detecting the moisture level accurately.
Testing
Once you have completed the adjustment procedure, it’s essential to test the moisture sensor to ensure it is functioning correctly. Testing the sensor involves running a drying cycle with a load of damp laundry and observing the drying time and the moisture level detected by the sensor. Make sure to note any irregularities or issues during the drying cycle.
If the problem persists after calibrating the moisture sensor, you may need to consult the user manual for further troubleshooting steps or consider contacting a professional technician for assistance.
Assessing Control Panel Malfunction
When your GE Sensor Dry dryer control panel malfunctions, it can be frustrating and confusing. Assessing the problem is the first step in finding a solution. Below, we break down common issues and provide troubleshooting tips to help you get your dryer back up and running.
Power Cycling
If your control panel is not responding or displaying error codes, power cycling the dryer may help reset the system. To do this:
- Unplug the dryer from the power source.
- Wait for at least 30 seconds.
- Plug the dryer back in and turn it on to see if the control panel is functioning properly.
Resetting The Controls
If power cycling doesn’t resolve the issue, you can try resetting the controls:
- Turn off the dryer and unplug it from the power source.
- Wait for a few minutes before plugging it back in.
- Once plugged in, press and hold the “Start” button for 5 seconds to reset the control panel.
Inspecting The Drum
When troubleshooting your GE Sensor Dry dryer, one crucial aspect to inspect is the drum. Issues with the drum can lead to performance problems and should be carefully examined to ensure smooth operation. Here’s how you can go about inspecting the drum to identify and resolve potential issues.
Foreign Object Removal
To begin the inspection, it’s important to check for any foreign objects that may have inadvertently found their way into the drum. These objects can cause the dryer to operate noisily or inconsistently. Perform a visual examination of the drum interior, and use a flashlight if needed, to look for any foreign objects such as coins, buttons, or small articles of clothing. If any foreign objects are found, carefully remove them to prevent potential damage to the dryer or its components.
Drum Support Evaluation
Another critical aspect of inspecting the drum is evaluating the drum support system. A worn-out or damaged drum support can lead to shaky and loud dryer operation. Begin by gently rotating the drum by hand to check for any excessive play or wobbling. If significant movement is observed, it may indicate a problem with the drum support. Additionally, listen for any unusual sounds that could point to an issue with the support system. Ensuring the drum is properly supported is essential for the overall performance and longevity of your GE Sensor Dry dryer.
Checking The Idler Pulley
When it comes to troubleshooting your GE Sensor Dry Dryer, the idler pulley is a crucial component to check. The idler pulley helps to maintain tension on the dryer belt, ensuring smooth and efficient operation. If the idler pulley is not functioning properly, it can lead to issues such as a noisy dryer or the drum not turning. Checking the idler pulley can help diagnose and resolve common dryer problems.
Lubrication
Proper lubrication of the idler pulley is essential for its smooth operation. Over time, the pulley may become dry, leading to increased friction and noise. Applying a small amount of dryer lubricant to the idler pulley’s bearing can help reduce friction and ensure it functions properly.
Replacing If Necessary
If the idler pulley shows signs of wear or damage, it may need to be replaced. Common signs of a faulty idler pulley include excessive noise, irregular rotation, or noticeable wear on the pulley itself. Replacing the idler pulley with a genuine GE replacement part can restore proper tension to the dryer belt and eliminate any related issues.
Frequently Asked Questions On Ge Sensor Dry Dryer Troubleshooting
What Are The Common Issues With Ge Sensor Dry Dryer?
The most common issues with the GE Sensor Dry dryer include overheating, not drying properly, and unusual noises. These issues can often be resolved through simple troubleshooting steps to ensure your dryer is working efficiently.
How Can I Resolve The Overheating Issue With Ge Sensor Dry Dryer?
To resolve the overheating issue with your GE Sensor Dry dryer, make sure the lint trap is clean, the vent is not blocked, and the dryer is not overloaded. Additionally, check for any obstructions in the venting system and ensure proper airflow to prevent overheating.
Why Is My Ge Sensor Dry Dryer Not Drying Clothes Thoroughly?
If your GE Sensor Dry dryer is not drying clothes thoroughly, it could be due to a clogged lint trap, obstructed vent, or a malfunctioning sensor. Clean the lint trap, check the vent for blockages, and ensure the sensor is functioning properly to resolve this issue.
How Do I Troubleshoot Unusual Noises From My Ge Sensor Dry Dryer?
Unusual noises from your GE Sensor Dry dryer may indicate a problem with the belt, drum bearings, or motor. Conduct a thorough inspection of these components, tighten any loose parts, and replace any damaged components to eliminate the unusual noises.
Conclusion
Troubleshooting GE Sensor Dry dryer issues can help enhance the appliance’s performance. By following the tips and techniques discussed in this blog post, you can effectively identify and resolve common problems. With proper maintenance and care, your GE Sensor Dry dryer can continue to operate efficiently, providing you with reliable drying results for your laundry needs.