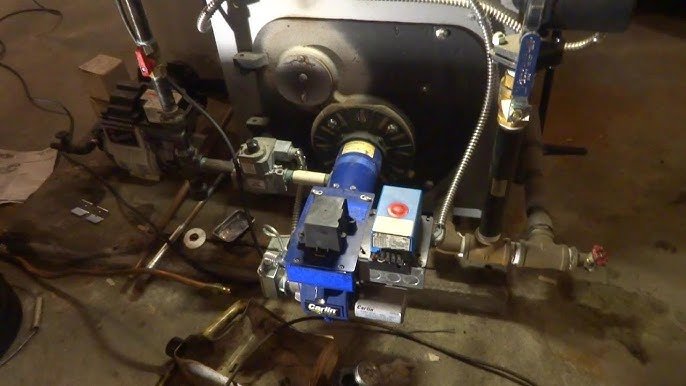
Check the gas supply and ensure the igniter is working. Verify there are no blockages in the burner.
Carlin gas burners are known for their reliability and efficiency, but like any appliance, they can encounter issues. Proper troubleshooting can help identify and resolve common problems quickly. Regular maintenance and inspection can prevent many issues from arising. Key areas to check include the gas supply, igniter functionality, and potential blockages in the burner.
Identifying these problems early can save time and money. Additionally, understanding the basic components and their functions can aid in troubleshooting. This guide aims to help you keep your Carlin gas burner running smoothly and efficiently. Always follow safety protocols during inspection and repair.
Introduction To Carlin Gas Burners
Carlin gas burners are essential for modern heating systems. They provide efficient and reliable heat. Understanding their functions can ensure smooth operations.
Importance In Heating Systems
Carlin gas burners are crucial in heating systems. They offer consistent and efficient heating. This ensures comfort during colder months.
- Energy Efficiency: Carlin burners use fuel efficiently.
- Reliability: They are known for their durability.
- Safety: Built with safety features to prevent accidents.
Common Issues Encountered
Even the best burners can have issues. Here are some common problems:
Problem | Cause | Solution |
---|---|---|
Burner Not Igniting | Faulty ignition system | Check and replace ignition components |
Weak Flame | Clogged nozzles | Clean or replace nozzles |
Uneven Heating | Blocked air filters | Clean or replace air filters |
Regular maintenance can prevent these issues. Always check the burner and its components.
Safety Precautions
Working with a Carlin gas burner requires utmost attention to safety. Proper safety precautions ensure your well-being and the efficient functioning of your burner. Below, we discuss essential safety measures.
Personal Protective Equipment
Always wear personal protective equipment (PPE) while troubleshooting. Essential PPE includes:
- Safety goggles to protect your eyes from sparks and debris.
- Heat-resistant gloves to shield your hands from burns.
- Durable work boots to safeguard your feet.
- Long-sleeved clothing to protect your skin.
Wearing PPE reduces the risk of accidents significantly.
Proper Ventilation
Ensure proper ventilation in your workspace. Gas burners can produce harmful fumes.
Follow these steps to maintain good ventilation:
- Open windows and doors to allow fresh air in.
- Use exhaust fans to expel fumes.
- Avoid working in confined spaces.
Proper ventilation prevents inhalation of toxic gases.
Safety Measure | Purpose |
---|---|
Wear Safety Goggles | Protects eyes from debris |
Use Heat-resistant Gloves | Shields hands from burns |
Ensure Proper Ventilation | Prevents inhalation of fumes |
Following these safety precautions helps ensure your safety while troubleshooting your Carlin gas burner.
Initial Diagnostics
Carlin gas burners are reliable, but they can have issues. Initial diagnostics can help you find the problem quickly. This guide will help you troubleshoot effectively.
Visual Inspection
Start with a visual inspection of the burner. Look for any obvious damage or wear.
- Check for any loose screws or parts.
- Inspect the burner for signs of corrosion.
- Ensure there are no obstructions blocking the burner.
Checking Connections
Next, check all the connections to ensure they are secure. Loose connections can cause malfunctions.
- Verify the gas supply connection is tight.
- Ensure the wiring connections are secure.
- Check the thermostat connections.
By performing these initial diagnostics, you can often find and fix the problem quickly.

Credit: www.hvacrmart.com
Ignition Problems
Ignition problems can disrupt the efficiency of your Carlin gas burner. These issues can lead to the burner not starting, causing delays and frustration. This section will explore common ignition problems and provide troubleshooting tips.
Spark Ignition Issues
The spark ignition system is crucial for starting the burner. If the spark is weak or absent, the burner will not ignite.
- Check the Spark Electrode: Ensure the electrode is clean and properly positioned.
- Inspect the Wiring: Look for any damaged or loose connections.
- Test the Ignition Module: Use a multimeter to ensure it is functioning correctly.
Pilot Light Troubles
The pilot light ignites the gas burner. Issues with the pilot light can prevent the burner from starting.
Problem | Solution |
---|---|
Pilot light won’t stay lit | Check the thermocouple; it might need replacement. |
Pilot light flickers | Adjust the flame or clean the pilot tube. |
Regular maintenance can prevent most ignition problems. Keep your burner clean and inspect it regularly.
Flame Stability
Ensuring flame stability in your Carlin gas burner is crucial. A stable flame means efficient combustion and safe operation. Unstable flames can cause poor performance and safety hazards.
Flame Sensor Cleaning
A dirty flame sensor can cause instability. Regular cleaning keeps it functional. Follow these steps:
- Turn off the burner and let it cool.
- Locate the flame sensor. It’s usually near the burner assembly.
- Remove the sensor carefully.
- Clean it using a fine-grit sandpaper.
- Wipe it with a clean cloth.
- Reinstall the sensor and restart the burner.
Adjusting Air Supply
Proper air supply ensures a stable flame. Too much or too little air affects combustion. Adjusting the air supply can help:
- Locate the air adjustment controls on your burner.
- Turn the burner on and observe the flame.
- Adjust the air intake slowly. Watch for changes in the flame.
- A stable flame is blue with a slight yellow tip.
- Make small adjustments and wait for the flame to stabilize.
- Once stable, note the settings for future reference.
Here is a quick reference table for air supply adjustments:
Flame Color | Adjustment Needed |
---|---|
Yellow | Increase air supply |
Blue with yellow tips | Perfect balance |
Blue with orange tips | Decrease air supply |

Credit: carlincombustion.com
Gas Supply Issues
Gas supply issues are common problems with Carlin gas burners. Consistent gas flow is crucial for optimal performance. Issues often arise due to gas pressure or faulty gas lines. Addressing these issues can help maintain efficiency and safety.
Checking Gas Pressure
Proper gas pressure is essential. Too high or too low pressure affects burner performance. Use a manometer to measure the gas pressure. Follow these steps:
- Turn off the burner and gas supply.
- Connect the manometer to the gas valve test port.
- Turn on the gas supply and burner.
- Read the manometer and compare it to the manufacturer’s specifications.
Adjust the gas pressure if it falls outside the recommended range. Use the pressure regulator on the gas valve. Consult the burner manual for guidance.
Inspecting Gas Lines
Gas line issues can disrupt the gas supply. Regular inspection is necessary. Check for any visible damage or leaks. Follow these steps for a thorough inspection:
- Turn off the gas supply.
- Visually inspect the gas lines for cracks or wear.
- Use a gas leak detector spray on the lines and connections.
- Look for bubbles which indicate a leak.
If you find leaks or damage, replace the gas lines immediately. Ensure all connections are tight and secure. Properly maintained gas lines ensure a stable gas supply.
Electrical Component Failures
Electrical component failures can disrupt your Carlin gas burner. These issues often cause the burner to stop working. Understanding how to troubleshoot these problems is essential. Below, we’ll delve into two main aspects: thermocouple testing and control module replacement.
Thermocouple Testing
The thermocouple is a key part of your burner. It senses the flame and signals the control module. If it fails, the burner won’t light. Here’s how to test it:
- Turn off the gas supply and power.
- Remove the thermocouple from the burner.
- Set a multimeter to millivolts (mV).
- Attach the multimeter probes to the thermocouple ends.
- Heat the thermocouple tip with a lighter.
- Check the multimeter reading.
A good thermocouple should read between 25-35 mV. If the reading is lower, replace the thermocouple. This simple test can save a lot of headaches.
Control Module Replacement
The control module manages the burner’s operations. If it fails, the burner won’t function. Follow these steps for replacing the control module:
- Turn off the power supply.
- Locate the control module in the burner unit.
- Disconnect all wiring from the module.
- Remove the screws holding the module in place.
- Install the new control module.
- Reconnect the wiring to the new module.
- Turn the power back on and test the burner.
Replacing the control module is straightforward. Ensure to follow the manufacturer’s instructions. This will help in avoiding any mistakes.

Credit: carlincombustion.com
Maintenance Tips
Keeping your Carlin gas burner in top shape ensures efficiency and safety. Proper maintenance can prevent unexpected breakdowns and extend the life of your burner. Follow these tips to keep your burner running smoothly.
Regular Cleaning
Regular cleaning of your Carlin gas burner is essential. Dirt and debris can clog the burner, leading to inefficient combustion.
- Turn off the gas supply before cleaning.
- Remove the burner cover to access internal parts.
- Use a soft brush to clean the burner components.
- Inspect for soot build-up and remove it carefully.
- Clean the air intake vents to ensure proper air flow.
Performing these steps monthly keeps your burner clean and efficient.
Scheduled Inspections
Scheduled inspections are crucial for identifying potential issues early. Regular checks can prevent costly repairs.
Inspection Task | Frequency |
---|---|
Check gas connections | Every 3 months |
Inspect burner flame | Monthly |
Examine electrical connections | Every 6 months |
Test safety controls | Yearly |
Maintain a log of these inspections to track the condition of your burner.
When To Call A Professional
Troubleshooting a Carlin gas burner can be a daunting task. Sometimes, you might need professional help. Knowing when to call a professional can save you time and ensure safety.
Complex Issues
Some problems with Carlin gas burners are too complex for DIY fixes. You should call a professional if you encounter these issues:
- Ignition Failures: The burner does not ignite.
- Erratic Flame: The flame flickers or burns unevenly.
- Control Issues: The burner does not respond to thermostat settings.
A professional can diagnose these complex issues quickly. They have the right tools and experience.
Safety Concerns
Working with gas burners involves safety risks. You should call a professional in these scenarios:
- Gas Leaks: You smell gas around the burner.
- Electrical Problems: You suspect wiring issues.
- Strange Noises: The burner makes unusual sounds.
Professionals know how to handle these hazards safely. This ensures your home remains safe and secure.
Issue | Reason to Call a Professional |
---|---|
Ignition Failures | Requires specialized tools and knowledge. |
Erratic Flame | Indicates deeper mechanical problems. |
Gas Leaks | Poses serious safety risks. |
Frequently Asked Questions
Why Is My Carlin Gas Burner Not Igniting?
Your Carlin gas burner might not ignite due to a faulty ignition system, gas supply issues, or blocked burners. Ensure the gas valve is open and the ignition system is working. Regular maintenance can prevent these problems.
How Do I Reset My Carlin Gas Burner?
To reset your Carlin gas burner, locate the reset button on the control panel. Press and hold it for a few seconds until the burner restarts. Refer to the user manual for specific instructions.
What Causes A Carlin Gas Burner To Short Cycle?
A Carlin gas burner may short cycle due to a dirty flame sensor, thermostat issues, or air flow problems. Clean the flame sensor and check the thermostat settings. Ensure proper ventilation around the burner.
Why Is My Carlin Gas Burner Making Noise?
Noises from your Carlin gas burner can be due to loose components, air in the gas line, or burner misalignment. Tighten any loose parts and check for air bubbles. If the problem persists, consult a professional.
Conclusion
Troubleshooting your Carlin gas burner can be simple with the right guidance. Regular maintenance ensures optimal performance. Follow the tips provided to prevent common issues. For persistent problems, consult a professional technician. Keep your burner running efficiently and safely. Stay proactive to avoid unexpected breakdowns.
Thank you for reading and happy troubleshooting!