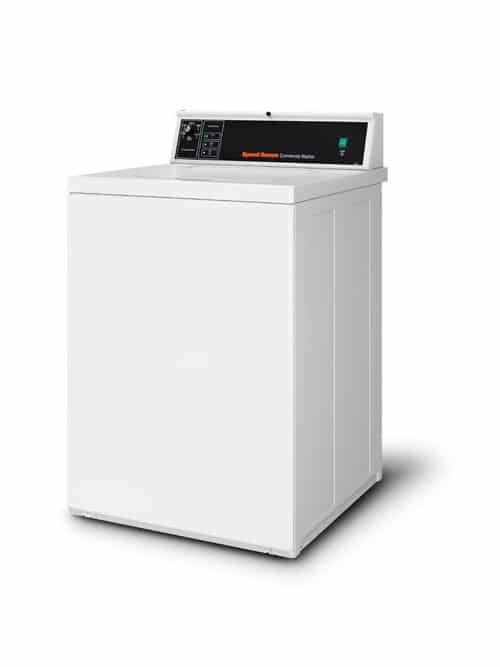
For troubleshooting a Speed Queen Commercial Heavy Duty Washer, check the power supply and ensure the door is closed properly. Examine the drain hose for clogs.
Speed Queen washers are known for their durability and efficiency in commercial settings. Proper maintenance and timely troubleshooting are essential to keep them running smoothly. Common issues include power supply problems, door latch malfunctions, and drainage blockages. Addressing these issues promptly can prevent costly repairs and downtime.
Simple checks like ensuring the washer is plugged in, the door is securely closed, and the drain hose is clear can resolve many problems. For more complex issues, consult the user manual or contact a professional technician. Regularly scheduled maintenance can also extend the life of your Speed Queen washer.
Common Issues
Speed Queen commercial heavy-duty washers are known for their durability and efficiency. Yet, even the best machines can face issues. Understanding common problems helps in maintaining the washer and ensuring its longevity. Here are some common issues you might encounter.
No Power
No power is a frequent issue with Speed Queen washers. It can stem from various causes. First, check if the washer is properly plugged in. Sometimes, the plug might be loose or not connected at all.
- Inspect the power cord for any visible damage. If you find frays or cuts, replace the cord immediately.
- Ensure the outlet is functional. Plug in another device to see if it works.
If everything seems fine with the plug and outlet, the issue might be with the circuit breaker. It might have tripped, cutting off power to the washer. Reset the breaker and see if that resolves the problem.
Another potential problem could be the washer’s internal fuse. If the fuse has blown, the washer won’t receive power. You may need to consult the manual or a technician to locate and replace the fuse.
Here’s a quick checklist to troubleshoot no power issues:
Step | Action |
---|---|
1 | Check the power plug and outlet |
2 | Inspect the power cord for damage |
3 | Reset the circuit breaker |
4 | Check and replace the internal fuse |
Water Not Filling
If your Speed Queen washer is not filling with water, several factors could be at play. Firstly, ensure the water supply valves are open. Both hot and cold water valves need to be fully turned on.
Next, check the inlet hoses. They could be kinked or blocked. Straighten any kinks and ensure the hoses are free of debris. It’s also wise to inspect the hose filters. If clogged, clean or replace them.
- Examine the water pressure. Low water pressure can prevent the washer from filling. Ensure your home’s water pressure meets the washer’s requirements.
- Check the water inlet valve. If defective, it won’t allow water to enter the machine. A multimeter can test the valve for continuity.
Another potential issue could be the washer’s control board. If the board is faulty, it might not signal the valve to open. This issue often requires professional diagnosis and repair.
Here’s a step-by-step guide to troubleshoot water filling issues:
Step | Action |
---|---|
1 | Ensure water supply valves are open |
2 | Inspect inlet hoses for kinks or blocks |
3 | Clean or replace hose filters |
4 | Check water pressure |
5 | Test and replace water inlet valve if necessary |
6 | Consult a technician for control board issues |
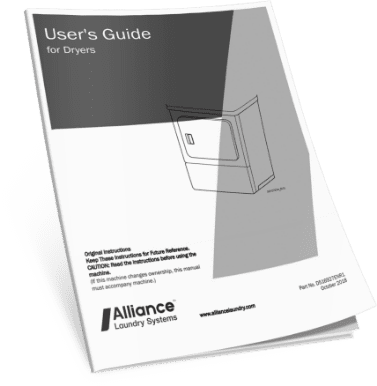
Credit: speedqueen.com
Error Codes
Speed Queen commercial heavy-duty washers are known for their durability and efficiency. But like any machine, they can encounter issues. Error codes help identify problems quickly. Knowing how to interpret these codes can save time and money. In this post, we’ll delve into understanding these codes and how to reset the machine.
Understanding Codes
Error codes are essential for diagnosing issues with Speed Queen washers. Each code points to a specific problem, allowing for quick troubleshooting.
Here are some common error codes and their meanings:
- E:dl – Door lock error.
- E:dL – Door unlock error.
- E:Lo – Low water error.
- E:Ho – High water error.
- E:dr – Drain error.
E:dl and E:dL indicate issues with the door mechanism. These errors could mean the door isn’t closing or opening properly. E:Lo and E:Ho relate to water levels. These errors may occur if the washer is not filling correctly or is overfilled. E:dr signals a problem with draining, which might be caused by a clogged hose or pump issue.
Here’s a quick reference table for these codes:
Error Code | Description |
---|---|
E:dl | Door lock error |
E:dL | Door unlock error |
E:Lo | Low water error |
E:Ho | High water error |
E:dr | Drain error |
Understanding these codes can help identify the problem quickly and efficiently.
Resetting The Machine
Resetting the machine can often resolve many issues. Here’s a step-by-step guide to reset your Speed Queen washer:
- Turn off the washer: Unplug the washer from the power source.
- Wait for a few minutes: Allow the machine to reset. Waiting for about 5 minutes should suffice.
- Plug the washer back in: Reconnect the washer to the power source.
- Restart the cycle: Turn on the washer and select a new wash cycle.
If the issue persists, you might need to perform a more detailed reset:
- Press and hold the power button for 10 seconds.
- Release the button and wait for a minute.
- Turn the washer back on and choose a new cycle.
Sometimes, the error code might still appear. In such cases, consult the user manual or contact a professional technician. Resetting the machine is a straightforward process, but it’s crucial to follow the steps carefully.
By knowing how to reset your washer, you can quickly address many common issues.
Drain Problems
Speed Queen Commercial Heavy Duty Washers are known for their durability and efficiency. Yet, even the best machines can face issues. One common problem is drain issues. Drain problems can disrupt the washing cycle and leave clothes soaking wet. Understanding these issues can help you fix them quickly and keep your washer running smoothly.
Clogged Hoses
Clogged hoses are a frequent cause of drain problems. When the hoses are clogged, water cannot exit the washer, causing it to back up. Follow these steps to check and clear clogged hoses:
- Turn off the washer and unplug it from the power source.
- Locate the drain hose at the back of the machine.
- Disconnect the hose from the washer and inspect it for blockages.
- Use a long brush or pipe cleaner to remove any debris inside the hose.
- Reattach the hose securely and plug the washer back in.
Sometimes, clogs can occur in the internal hoses within the washer. In this case, you may need to open the washer’s back panel:
- Remove the screws holding the back panel in place.
- Inspect all internal hoses for blockages.
- Clear any debris you find using a brush or pipe cleaner.
- Reassemble the back panel and test the washer.
Regularly checking and cleaning the hoses can prevent future clogs. This simple maintenance step ensures your Speed Queen washer drains properly every time.
Pump Malfunctions
Pump malfunctions can also lead to drain problems. The pump is responsible for pushing water out of the washer. If it fails, water remains inside. Check for these signs of pump issues:
- Unusual noises during the drain cycle.
- Water remaining in the drum after the cycle completes.
- Error codes on the washer’s display panel.
To address pump malfunctions:
- Turn off and unplug the washer.
- Access the pump by removing the washer’s back panel.
- Inspect the pump for visible damage or blockages.
- Remove any debris and check the pump’s impeller for free movement.
- If the pump is damaged, replace it with a new one.
Regular maintenance can prevent pump issues. Ensure the pump area is clean and free of lint and other debris. This keeps your Speed Queen washer running efficiently and extends its lifespan.
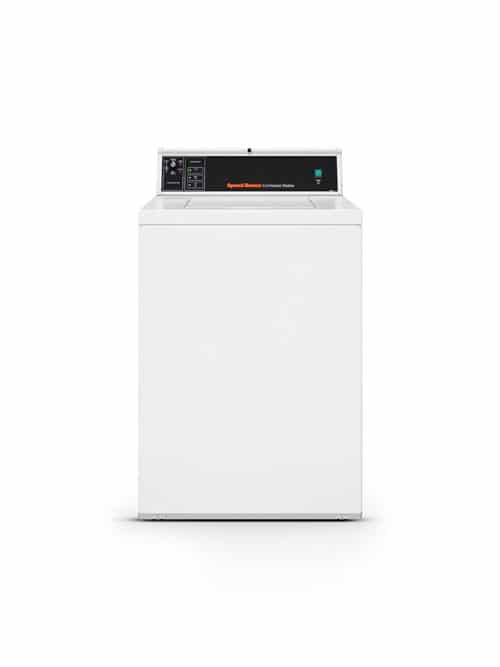
Credit: speedqueenprofessional.com
Spin Cycle Troubles
Speed Queen commercial heavy duty washers are known for their reliability. Yet, users sometimes face spin cycle troubles. Common issues include the washer not spinning or making excessive noise. Understanding these problems can help in troubleshooting and fixing them efficiently.
No Spin
If your Speed Queen washer is not spinning, several factors might be responsible. Check these possible causes:
- Lid Switch: Ensure the lid is closed properly. A faulty lid switch can prevent spinning.
- Drive Belt: Inspect the drive belt. If it’s worn or broken, it needs replacing.
- Motor Coupling: Check the motor coupling for damage. A broken coupling stops the spin cycle.
- Spin Timer: Verify the timer is working. A faulty timer can hinder the spin cycle.
Use this table for a quick troubleshooting guide:
Problem | Possible Cause | Solution |
---|---|---|
No Spin | Lid Switch | Ensure the lid is closed |
No Spin | Drive Belt | Replace if worn or broken |
No Spin | Motor Coupling | Check and replace if damaged |
No Spin | Spin Timer | Replace the faulty timer |
Excessive Noise
Excessive noise during the spin cycle can be alarming. Common reasons include:
- Loose Items: Check for loose items in the drum. Coins, buttons, or debris can cause noise.
- Unbalanced Load: Ensure the load is balanced. Uneven weight distribution leads to noise.
- Worn Bearings: Listen for a grinding sound. Worn bearings need replacement.
- Damaged Drive Pulley: Inspect the drive pulley. If damaged, it can cause a loud noise.
Here is a table to assist with diagnosing noise issues:
Noise Type | Possible Cause | Solution |
---|---|---|
Rattling | Loose Items | Remove items from the drum |
Banging | Unbalanced Load | Redistribute clothes evenly |
Grinding | Worn Bearings | Replace bearings |
Squeaking | Drive Pulley | Inspect and replace if damaged |
Taking prompt action can prevent further damage to your Speed Queen washer. Regular maintenance ensures a longer lifespan and efficient performance.
Temperature Control
Speed Queen Commercial Heavy Duty Washers are famous for their durability and performance. But even the best machines can face issues, especially with temperature control. Proper temperature control ensures clothes are washed at the correct temperature, enhancing cleaning efficiency and fabric care. Let’s explore some common temperature control issues and how to troubleshoot them.
Cold Water Only
If your washer is using cold water only, it might be due to several reasons. Identifying the cause helps in resolving the issue efficiently.
- Check Water Supply: Ensure both hot and cold water faucets are turned on.
- Inspect Hoses: Verify that the hoses are connected to the correct faucets.
- Temperature Selector Switch: This switch might be defective. Test it with a multimeter for continuity.
- Control Board Issues: A malfunctioning control board can also result in cold water only. Inspect for any visible damage or burnt components.
Below is a table summarizing the troubleshooting steps:
Issue | Possible Cause | Solution |
---|---|---|
Cold Water Only | Water Supply Issue | Check Faucets |
Cold Water Only | Hose Connection | Verify Connections |
Cold Water Only | Temperature Selector Switch | Test and Replace |
Cold Water Only | Control Board | Inspect and Replace |
Overheating Issues
Overheating can damage clothes and the washer itself. Address this issue promptly to avoid further complications.
- Thermostat Malfunction: A faulty thermostat can cause water to overheat. Test it with a multimeter and replace if necessary.
- Heating Element Problems: A damaged heating element might not regulate temperature properly. Inspect for any visible damage or signs of wear.
- Temperature Sensor Issues: The sensor might be giving incorrect readings. Test and replace if it’s not working correctly.
- Control Board Faults: Sometimes, the control board sends incorrect signals. Inspect the board and replace it if needed.
Here’s a table for quick reference:
Issue | Possible Cause | Solution |
---|---|---|
Overheating | Thermostat Malfunction | Test and Replace |
Overheating | Heating Element Problems | Inspect and Replace |
Overheating | Temperature Sensor Issues | Test and Replace |
Overheating | Control Board Faults | Inspect and Replace |
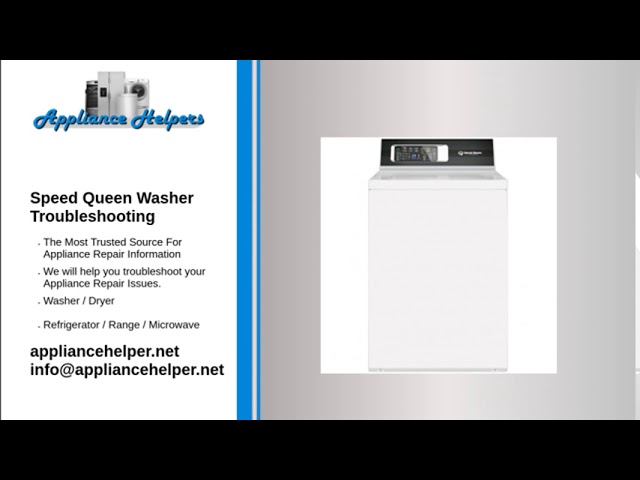
Credit: www.youtube.com
Electrical Issues
Speed Queen commercial heavy-duty washers are known for their durability and performance. However, electrical issues can arise, causing the machine to malfunction. Identifying and troubleshooting these issues can help maintain the washer’s efficiency and extend its lifespan. This section will delve into common electrical problems, focusing on faulty wiring and control board problems.
Faulty Wiring
Faulty wiring is a common issue in commercial washers. It can lead to various problems like the machine not starting or unexpected shutdowns. Here are some signs and steps to troubleshoot faulty wiring:
- Machine won’t start: Check the power cord and plug for any visible damage. Replace if necessary.
- Intermittent power loss: Inspect the wiring inside the machine. Look for loose or frayed wires.
- Burning smell: This could indicate a short circuit. Turn off the power and examine the wiring.
Use a multimeter to test the continuity of the wires. Follow these steps:
- Unplug the washer from the power source.
- Remove the back panel to access internal wiring.
- Set the multimeter to the continuity setting.
- Touch the probes to each end of the wire.
- If the multimeter beeps, the wire is good. If not, replace the wire.
Regular maintenance of the wiring can prevent many electrical issues. Ensure all connections are tight and secure. Replace any damaged wires immediately to avoid further problems.
Control Board Problems
The control board is the brain of the washer. It manages all the electrical functions. When it fails, the machine can exhibit erratic behavior. Here are some symptoms and troubleshooting steps for control board issues:
- Unresponsive buttons: The washer does not respond when buttons are pressed. This could indicate a control board issue.
- Error codes: The display shows error codes that do not go away even after resetting the machine.
- Cycles not completing: The washer stops in the middle of a cycle without any apparent reason.
To troubleshoot the control board:
- Turn off the power and unplug the machine.
- Remove the control panel cover to access the control board.
- Inspect the board for any visible damage like burnt components or loose connections.
- Use a multimeter to check the voltage at various points on the board as per the manufacturer’s specifications.
- If the board is damaged, replace it with a new one following the manufacturer’s instructions.
Regular inspection of the control board can help identify issues before they escalate. Keep the board clean and ensure all connections are secure to maintain optimal performance.
Maintenance Tips
Speed Queen commercial heavy-duty washers are known for their durability and efficiency. To keep them performing at their best, regular maintenance is key. Proper upkeep helps prevent issues and prolongs the machine’s lifespan. Here are some essential maintenance tips for troubleshooting your Speed Queen washer.
Regular Cleaning
Keeping your Speed Queen washer clean is vital for optimal performance. Regular cleaning can prevent buildup that affects washing quality. Here are some steps:
- Wipe down the exterior with a damp cloth to remove dust and grime.
- Clean the detergent dispenser monthly to avoid soap residue.
- Run an empty wash cycle with hot water and vinegar every month to clean the drum.
To clean the lint filter and ensure it operates efficiently:
- Locate the lint filter and remove it.
- Rinse the filter under warm water.
- Reinstall the filter once it’s dry.
Check the hoses for any signs of wear or leaks. Replace them if necessary. Maintaining a clean washer prevents mold and mildew, ensuring your laundry smells fresh.
Proper Usage
Using your Speed Queen washer correctly can prevent many common issues. Follow these proper usage tips:
- Do not overload the washer. Overloading can strain the motor and reduce washing efficiency.
- Use the correct detergent. High-efficiency (HE) detergent is recommended.
- Balance the load. An unbalanced load can cause excessive vibration and noise.
To ensure proper usage, consider these points:
Action | Frequency |
---|---|
Check and clean the lint filter | Monthly |
Inspect hoses for wear | Every 6 months |
Run an empty hot water cycle | Monthly |
Following these tips ensures your Speed Queen washer runs smoothly. Proper usage and regular maintenance keep your machine in top condition.
When To Call For Help
Speed Queen commercial heavy-duty washers are known for their reliability and durability. But even the best machines can encounter issues. Knowing when to call for professional help can save you time and money. This guide helps identify major problems and find the right technician.
Identifying Major Issues
It’s crucial to recognize the signs that indicate major issues with your Speed Queen washer. Addressing these problems promptly can prevent further damage.
- Unusual Noises: Banging, grinding, or screeching sounds during operation indicate mechanical issues.
- Water Leakage: Puddles around the washer suggest a leak. This could be due to faulty hoses or seals.
- Electrical Problems: Flickering lights or power outages during cycles could signal electrical faults.
- Drum Issues: If the drum doesn’t spin or agitates improperly, there might be belt or motor problems.
- Error Codes: Modern washers display error codes. Refer to the manual to understand these codes.
If you notice any of these signs, it’s time to take action. Ignoring these problems can lead to more severe damage and costly repairs.
Finding A Technician
Once you’ve identified a major issue, finding a qualified technician is the next step. Here’s how to do it effectively:
- Research: Look for technicians specializing in Speed Queen washers. Check online reviews and ratings.
- Certifications: Ensure the technician holds relevant certifications. This guarantees they have the required skills and knowledge.
- Experience: Choose a technician with extensive experience in commercial washer repairs.
- Cost Estimates: Request a detailed estimate before the repair. This helps you avoid unexpected charges.
- Warranty: Ask if the technician offers a warranty on their work. This provides peace of mind.
Finding the right technician ensures your washer gets the best possible care. A well-maintained washer lasts longer and performs better.
Frequently Asked Questions
How Do I Reset My Speed Queen Washer?
To reset your Speed Queen washer, unplug it for one minute. Plug it back in and press the power button. This should reset the machine.
Why Is My Speed Queen Washer Not Spinning?
Check if the load is balanced. Uneven loads can cause spinning issues. Also, ensure the lid is closed properly.
What Does Error Code E Dl Mean?
Error code E dL indicates a door lock issue. Check if the door is closed securely. If the problem persists, consult the user manual.
How Do I Clean My Speed Queen Washer?
Use a washing machine cleaner monthly. Run a hot water cycle with the cleaner. Wipe the drum and door gasket afterward.
Conclusion
Troubleshooting your Speed Queen commercial heavy-duty washer can save you time and money. Follow these tips to identify common issues. Regular maintenance ensures optimal performance and longevity. If problems persist, consult a professional technician. Keep your washer running smoothly and efficiently with proper care and attention.